ENTISE - Entwicklung einer Natrium-Ionen-Batterie
EntiSE - Natrium-Ionen-Batterien Aufbau
Ressourcen sind beschränkt und heutige Batteriematerialien stehen in der Kritik, gefährlich zu sein. Wie interessant vor diesem Hintergrund der Gedanke klingt, Energiespeicher aus ungefährlichen und allseits verfügbaren Materialien herstellen zu können! Diese Möglichkeit erforschen wir zusammen mit Partnern im Projekt „Entise“. Das BMBF-Forschungsprojekt startete mit dem Ziel, eine leistungsfähige, kostengünstige und umweltfreundliche Zellchemie für Natrium-Ionen-Batterien zu entwickeln und in industriell einsetzbare Zellformate zu überführen.
Natrium-Ionen-Batterien sind vielversprechend für eine nachhaltige und ressourcenschonende Zukunft der Energiespeicherung. Natrium ist nicht nur kostengünstig und reichlich vorhanden, sondern auch sicher und einfach zu recyceln. Die Herausforderung besteht darin, diese Technologie in industriell verwertbare und skalierbare Zellen zu übertragen. Hier setzt das Projekt ENTISE (Entwicklung der Natrium-Ionen-Technologie für Industriell skalierbare Energiespeicher) an.
Verbesserung der Speicherkapazität und Zyklenstabilität
Im Mittelpunkt von ENTISE steht die Weiterentwicklung bestehender Materialkonzepte und Prozesse. Technologisch soll insbesondere die Speicherkapazität von Kathode und Anode verbessert werden, wozu die eingesetzten Materialien einschließlich der verwendeten Elektrolyte optimiert werden müssen. Darüber hinaus soll die Zyklenstabilität, also die Fähigkeit der Zellen, auch nach mehrmaligem Laden und Entladen eine stabile Leistung zu gewährleisten, durch die Entwicklung neuer Materialien, optimierter Elektrodenmaterialien und Beschichtungen verbessert werden.
In Zusammenarbeit zwischen den Industrie- und Forschungspartnern erfolgt dann in der letzten Projektphase die Hochskalierung der Einzelkomponenten und der Transfer vom Labor in den vorindustriellen Maßstab (Pilotierung). Am Ende wird eine eine Kleinserie von Rundzellen stehen, die eine belastbare Eigenschaftsbewertung in praxisrelevanten Einsatzszenarien wie in stationären Speichern ermöglicht. Eine begleitende technisch-ökonomische und ökologische Bewertung rundet das Projekt ab. Zentraler Bestandteil ist dann die Herstellung ausreichender Mengen, um einzelne belastbare Labormuster bis hin zu Prototypen im Rundzellendesign aufzubauen.
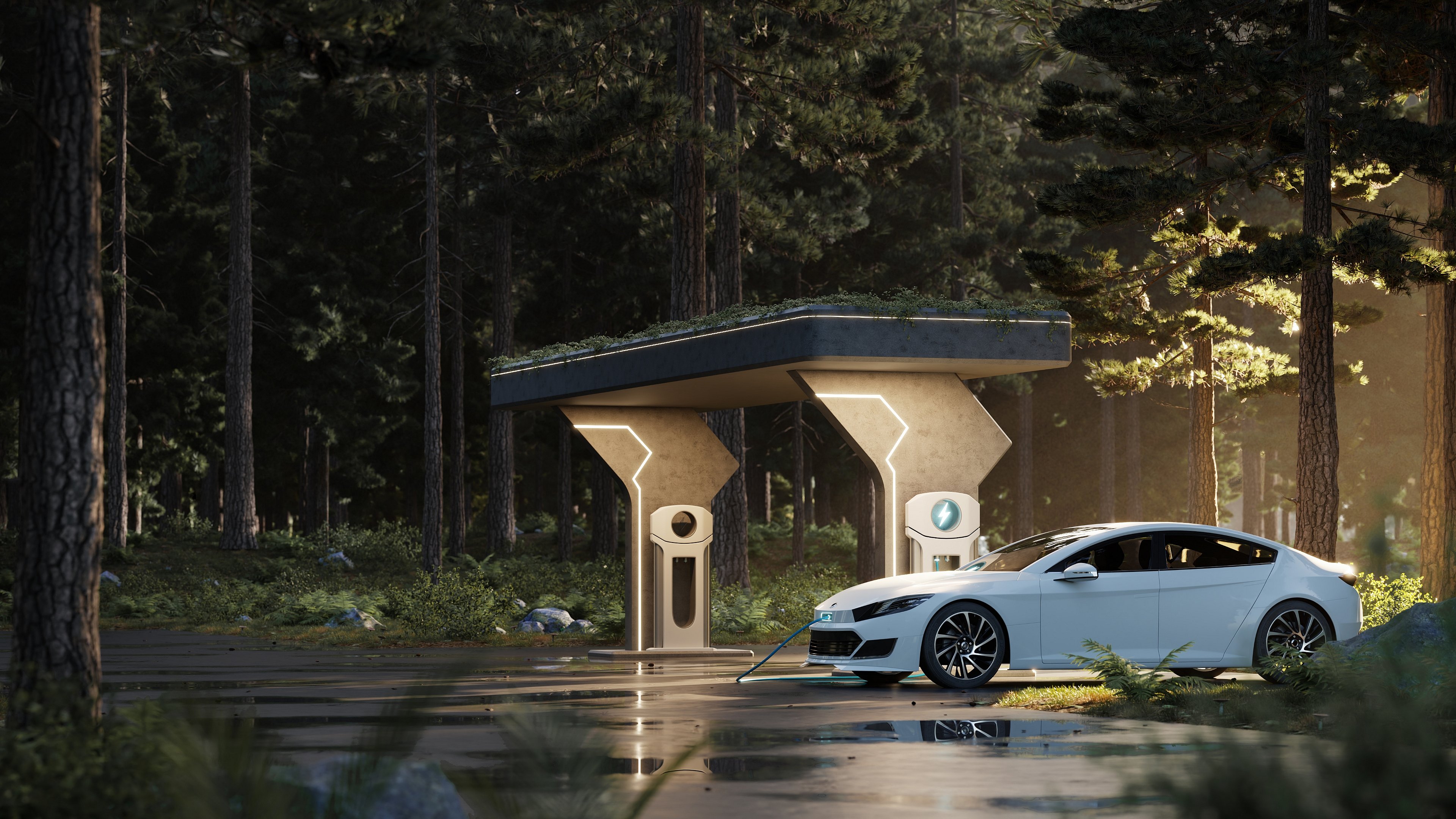
Vom Prototypen zu marktreifen Zellen für Elektrofahrzeuge oder Heimspeicher
Unser F&E-Team wird mit den Projektpartnern geeignete Materialsysteme für die Anwendung als Kathodenmaterialien definieren, erforschen und für Anwendungsuntersuchungen bereitstellen. Wir erarbeiten Lösungen zur Skalierung des Prozesses, welche im Netzwerk des Projektes untersucht werden: VARTA Microbattery GmbH (Initiator und Projektkoordinator) ist zuständig für die Evaluation am Markt verfügbarer Materialien, sowie für die Herstellung von Referenz- und Prototypzellen; die VARTA Storage GmbH übernimmt das Zellbenchmarking, sowie die Use-Case Prüfung für stationäre Speicheranwendungen.
Weitere Projektpartner sind das Helmholtz Institut Ulm; die Humboldt-Universität zu Berlin; die Universität Freiburg (Freiburger Materialforschungszentrum); das Zentrum für Sonnenenergie- und Wasserstoff-Forschung Baden-Württemberg; die Justus-Liebig-Universität Gießen; das Karlsruher Institut für Technologie (Institut für Nanotechnologie, Battery and Electrochemistry Laboratory); das Forschungszentrum Jülich; EurA AG; E-Lyte Innovations GmbHund Karlsruher Institut für Technologie (Institute for Applied Materials - Energy Storage Systems).
Ablauf der Entwicklung einer Natrium-Ionen-Batterie
Geeignete Schichtoxide werden als Aktivmaterialien definiert und anschließend skaliert. Innerhalb des Projektes versuchen wir, Na-Ionen-Aktivmaterialien mit den erforderlichen Zielvorgaben (Morphologie und Zusammensetzung) zu generieren und ein geeignetes Herstellungsverfahren unter Zuhilfenahme des Pulsationsreaktors zu entwickeln. Die generierten Muster werden den Partnern für Anwendungstests zur Verfügung gestellt. Auf Basis dieser Anwendungsuntersuchungen sollen die Aktivmaterialsysteme bei uns systematisch erforscht, weiterentwickelt und skaliert werden. Zusammen mit unserem Mutterkonzern IBU-tec beteiligen wir uns mit der Entwicklung und Herstellung des Kathodenaktivmateriales in einer Kombination aus Prozessschritten in Pulsationsreaktoren sowie der thermischen Nachbehandlung im Drehrohrofen.
In den initialen Stufen des Projektes sind Leistungsparameter festgelegt sowie ein konkretes Natrium-Manganoxid -Kathodenaktivmaterial ausgewählt worden – wahlweise mit oder ohne Additive. Bei zufriedenstellenden Ergebnissen und ausreichender Performance wird sich ein Scale-up für die Produktion des Kathodenaktivmateriales anschließen, unter Beibehaltung der in den Technikums-Anlagen erreichten Eigenschaften. Anschließend findet die energetische Optimierung des Prozesses, um eventuelle Produktionskosten zu senken, statt.