ProLit – Trockenbeschichtung von Kathoden
ProLit - Trockenbeschichtung für Batterien
Heutigen Batterien und Superkondensatoren sind mit Elektroden (Anoden und Kathoden) gefüllt, die meist nasschemisch prozessiert werden. Dies bedeutet, dass bei der Herstellung der Elektroden eine in einem organischen Lösungsmittel dispergierte Paste auf dem Stromsammler aufgetragen und anschließend getrocknet werden muss. In der Industrie eingesetzte Trocknungslinien sind lang und energieintensiv im Betrieb, dazu kommen notwendige Peripheriegeräte, um giftige Lösungsmittel aus der Abluft zu entfernen und Umweltvorschriften einzuhalten.
Trockenbeschichtung von Kathoden
Die Trockenbeschichtung ist ein neues Herstellungsverfahren, welches auf einem Trockenfilm basiert, der den Einsatz giftiger Lösungsmittel überflüssig macht. Aus ökologischer Sicht verspricht der Verzicht auf Lösungsmittel eine hohe Energieeffizienz durch geringeren Energieverbrauch im optimierten Prozess und kürzere Prozessdauer. Generell können durch die Trockenbeschichtung die CO2-Bilanz und die Wirtschaftlichkeit der Batteriezellproduktionen gesteigert werden.
Die Trockenbeschichtung von Kathoden (für Lithium-Ionen-Batterie, LIB) steht im Mittelpunkt des Forschungsprojekt ProLiT (Forschungsprojekt zur Prozess- und Materialentwicklung von Lithium-Ionen-Batteriekathoden für die großtechnische Trockenbeschichtung). Das Projekt ist Teil der Förderrichtlinie „Batteriematerialien für zukünftige elektromobile-, stationäre- und weitere industrierelevante Anwendungen (Batterie 2020 Transfer)“ im Rahmenprogramm „vom Material zur Innovation“ des Bundesministeriums für Bildung und Forschung (BMBF) und wurde vor 3 Jahren (1. Januar 2022) begonnen.
ProLiT kombiniert die Entwicklung von LIB-Materialien (Kathoden- und Bindermaterialien) mit der Prozess- und Anlagenentwicklung mit dem Ziel, skalierbare und wettbewerbsfähige Prozesse und Produkte in die Industrie zu transferieren. Wesentlich für die Trockenbeschichtung ist die Herstellung einer trockenen Pulvermischung aus dem entsprechenden Aktivmaterial, leitfähigem Additiv und thermoplastischen Bindemittel. Entscheidend ist dabei die homogene Verteilung der Komponenten, wodurch die Mischungen mit einem Bindemittelanteil von fünf Gewichtsprozent oder weniger zu einer stabilen Elektrode verarbeitet werden können. In einem weiteren Verfahrensschritt wird diese Pulvermischung dann auf den Stromkollektor (Aluminiumfolie auf der Kathodenseite) übertragen und anschließend durch thermomechanische Behandlung (mit Walzenkalender) dauerhaft fixiert. Die mechanisch stabilen Elektroden werden dann anschließend zu Testzellen (Knopf- oder Pouchzellen) verbaut und elektrochemisch charakterisiert.
IBUvolt-Expertise
Mit unserer Expertise in der thermischen Verfahrenstechnik stehen wir als Lithium-Eisenphosphat (LFP)-Kathodenmaterial Hersteller am Anfang der Entwicklungskette. Ziel der Materialsynthese und -entwicklung ist es, LPF-Materialien für den Trockenbeschichtungsprozess anzupassen und zu optimieren, um die erforderlichen Elektrodeneigenschaften (gute Haftung, Dichte, Porosität, Leitfähigkeit) zu erreichen. Dabei ist das Ziel die Entwicklung eines Materials, welches sich gut mit dem leitfähigen Additiv vermischt, keine Agglomerate verursacht und anschließend eine gute Fibrillierung ermöglicht.
Unser kommerziell erhältliches IBUvolt® LFP400 und einige R&D Grades wurden bereits getestet, um die Projektanforderungen zu erfüllen. Dabei stellte sich das IBUvolt® LFP400 als sehr guter Kandidat für die Trockenbeschichtung heraus. Außerdem zeigten bestimmte R&D Grades eine gute Prozessierbarkeit, eine mühelose Aluminiumfolienbeschichtung und eine gute Kapazität.
Ein weiteres Alleinstellungsmerkmal des Projekts (neben Materialentwicklung und Prozessoptimierung) ist die systematische Entwicklung eines leistungseffizienten Industrieprozesses in Verbindung mit der Produktentwicklung. Dabei erfolgt die wechselseitige Betrachtung von skalierbaren Mischprozessen zur Materialstrukturierung diskontinuierlich im Batch-Mischer und kontinuierlich im Extruder, der kontinuierlichen Dosierung des Pulvers sowie des eigentlichen und mehrstufig abgebildeten Beschichtungsprozesses in der speziell für ProLiT angepassten Vierwalzen-Kalander.
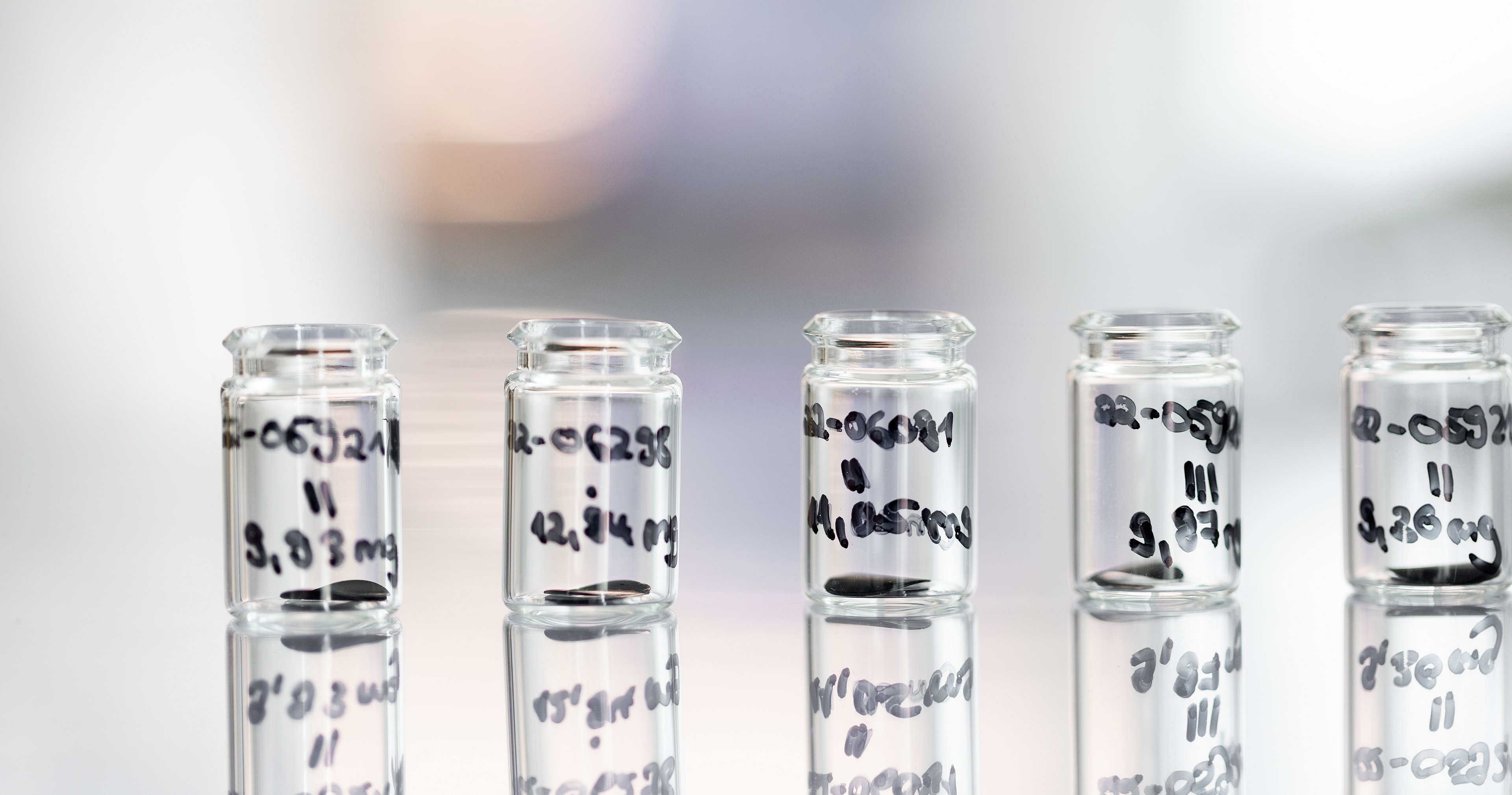
Das ProLit Projektkonsortium
Die Projektpartner setzen sich aus Materialherstellern, Maschinen- und Anlagenbauern, Zellherstellern und Wissenschaftlern aus der deutschen Industrie- und Forschungslandschaft zusammen: Customcells Holding GmbH, Daikin Chemical Europe GmbH (Hersteller der Bindematerials), Matthews International GmbH Department Saueressig Engineering, Institut für Partikeltechnik/ BLB der TU Braunschweig, MEET Batterieforschungszentrum der Westfälischen Wilhelms-Universität Münster (WWU) und als assoziierte Partner: die Coperion K-tron Deutschland GmbH, die Maschinenfabrik Gustav Eirich GmbH & Co. KG, Umicore N.V (produziert das Ni-reiche Nickel-Mangan-Kobalt-Material, NMC) sowie die Bayerische Motoren Werke AG.